In April 2021 Continental Tyres purchased a Delta S3 simulator from Ansible Motion. The tyre manufacturer has now put its new driving simulator into operation, which will be used for new and further tyre developments, especially in its original equipment business.
Thanks to its high manoeuvrability, with all six degrees of freedom, the simulator can provide Continental’s professional test drivers with subjective driving impressions that the company says are comparable to those gained from tyre tests on a real test track – saving raw materials and shortening development times. An intensive test phase lasting around 12 months preceded the operational phase.
How the virtual tests work
The simulator calculates the exact driving dynamics parameters for the tyres and the corresponding test vehicle. Continental loads the relevant tyre model for the customer’s specific vehicle model into the simulator. The tyre model contains precise information on the tyre design, tread, and rubber compound. The test driver thus drives a dedicated tyre model for a specific vehicle model variant, as was previously the case on the physical test track.
Tyres for all vehicle and drive variants, for passenger cars and commercial vehicles, whether for electric, hybrid or combustion-engine vehicles, can be evaluated in the simulator. The advantage is that the tyre parameters can be adjusted digitally at any time. This means that test drives can be repeated at short intervals, and subjective drive impressions can be compared directly with each other.
Thanks to its extensive motion platform (4m long, 5m wide) which features a maximum acceleration of 12m per second, the test drivers experience all six degrees of freedom of the vehicle dynamics – just like in a real vehicle on a physical test track – including the longitudinal and lateral movements, the stroke movement, and the yaw, pitch and roll of a vehicle. Professional test drivers are trained to incorporate these subjective driving impressions into the development process. This experience is essential for achieving the exact tyre set-up required by the vehicle manufacturers for the particular vehicle model.
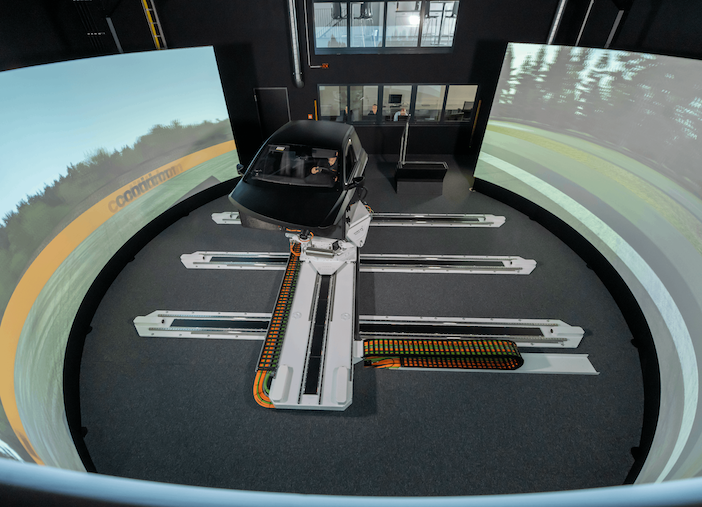
The driving simulator is located on the grounds of the Contidrom, the tyre test facility which has been an important part of Continental’s research and development department since its foundation in 1967. Car, truck, and motorcycle tyre are tested intensively at the facility.
“With our driving simulator, we evaluate and optimize a tyre before we physically build it for the first time,” explained Julian Kroeber, who is responsible for the tyre simulator at Continental. “This allows us to further optimise our development process. It also saves a lot of time for our customers.”

New materials that are being used in a tyre for the first time can also be tested extensively in the new simulator. Testing is particularly important, because every time an approved material in a tyre is replaced by a new one, the new material’s properties and interactions with other materials must be thoroughly investigated. Continental thus ensures that its tyre s later meet the highest performance criteria for safety-related properties as well as for other important aspects such as rolling resistance and noise development.
“Virtual development methods enable us to offer solutions even more efficiently and more precisely tailored to the needs and requirements of our customers. Virtual test kilometers also play a major part in conserving valuable resources,” added Bernd Korte, head of passenger tire development for Continental’s original equipment business. “With our new driving simulator, we can shorten development times and optimise the use of resources in production and logistics.”
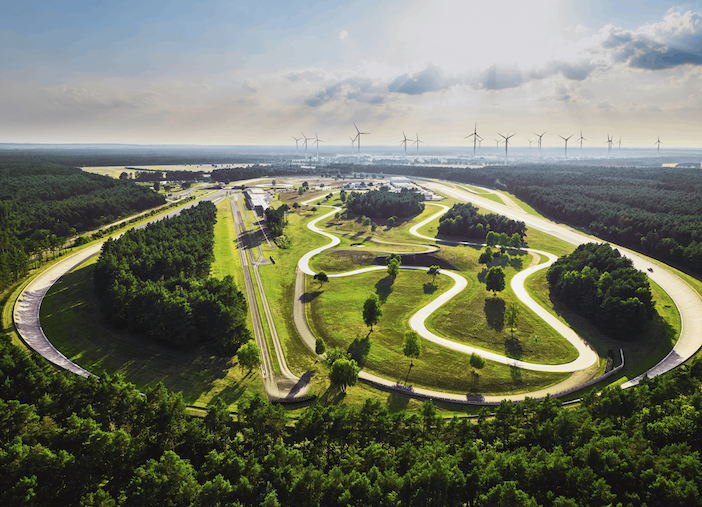