GKN Automotive, a supplier of automotive all-wheel drive and electric driveline technology and systems, has announced that by the end of this month it will have delivered its one millionth eDrive system. The company states that demand for its expanding eDrive portfolio, which encompasses a range of driveline technologies for electrified vehicles, has increased “markedly” over recent years. The company currently has five major mass-production projects in progress for eDrive in China and Europe.
GKN Automotive has been involved in advanced eDrive technologies since 2002, beginning with transmissions, then eMotor and transmission systems, through to fully integrated motor, gearbox and inverter systems, with OEM clients including BMW, Mitsubishi, Porsche and Volvo.
Hannes Prenn, COO of GKN Automotive ePowertrain, commented, “It is always a proud moment when GKN Automotive reaches a significant production milestone, and this one is particularly significant as it underlines our leadership in the fast-growing eDrive segment. The strength and breadth of our current eDrive order book is a testament to our heritage of eDrive innovation, development and integration, as well as our ability to meet the exacting quality and production targets set by our customers.”
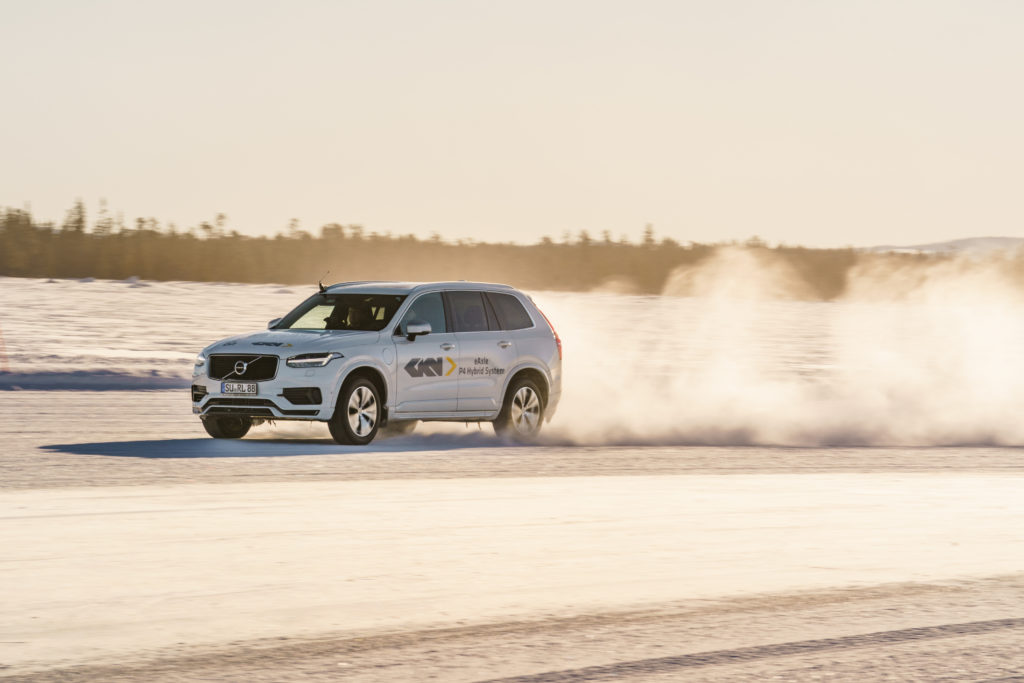
ACeDrive – the next-generation of eDrive
GKN Automotive is collaborating with Drive System Design and the UK’s University of Nottingham on an £8 million project to design and develop the world’s lightest and most efficient electric vehicle powertrain suitable for the volume market. The initiative is match-funded by the Advanced Propulsion Centre (APC), an organisation created by the UK Government’s Automotive Council to fund UK-based research and development projects, aimed at developing low-carbon emission powertrain technologies.
ACeDrive (Advanced Cooling and Control of High Speed e-Drive) aims to achieve the level of technology and performance outlined in the Automotive Council’s roadmap for 2030. The core targets for the resulting eDrive technology are a 25% reduction in both packaging size and cost, a 20% drop in weight, and a 10% increase in efficiency compared to current equivalents, and production readiness by 2023.