Lotus Cars has built the first extruded and bonded aluminium chassis at its new manufacturing facility at Hurricane Way, Norwich, 10 miles from its headquarters in Hethel, UK. The chassis is designed for the Lotus Elise, and has been built for validation and quality checking of the new manufacturing process. Although not destined for a final vehicle, the chassis will remain at the factory for testing. Lotus says that as chassis manufacturing volumes at the facility grow steadily over the next few months, it will help ensure that the processes adhere to the globally recognised quality standards expected.
The 12,300m2 facility has the capacity to build several thousand chassis per year. During 2021 the company expects that around 1,500 units will produced at the site for the Lotus Elise, Exige and Evora models. Set to employ 125 highly skilled operatives, technicians and engineers, the site also houses the welding and fabrication of sub-frames, suspension components and other key parts for Lotus cars.
Lotus announced in July 2020 that as part of its expansion programme, the company had outgrown its existing facilities in Worcester and Norwich, and so would bring together both production processes into one new combined location – the Hurricane Way facility. Tooling has already been upgraded in readiness for a new range of Lotus sports cars to be launched in the coming years.
David Hewitt, executive director of operations at Lotus Cars, said: “The production of this first lightweight chassis is a significant landmark for the new Hurricane Way facility. In parallel, we are close to finishing our new assembly facility at our Hethel HQ. By the end of the year, the whole of Lotus’s sports car manufacturing facilities and processes will be either new or vastly improved. This will give us solid foundations to maintain our leadership in the rapidly changing low-volume automotive assembly industry.”
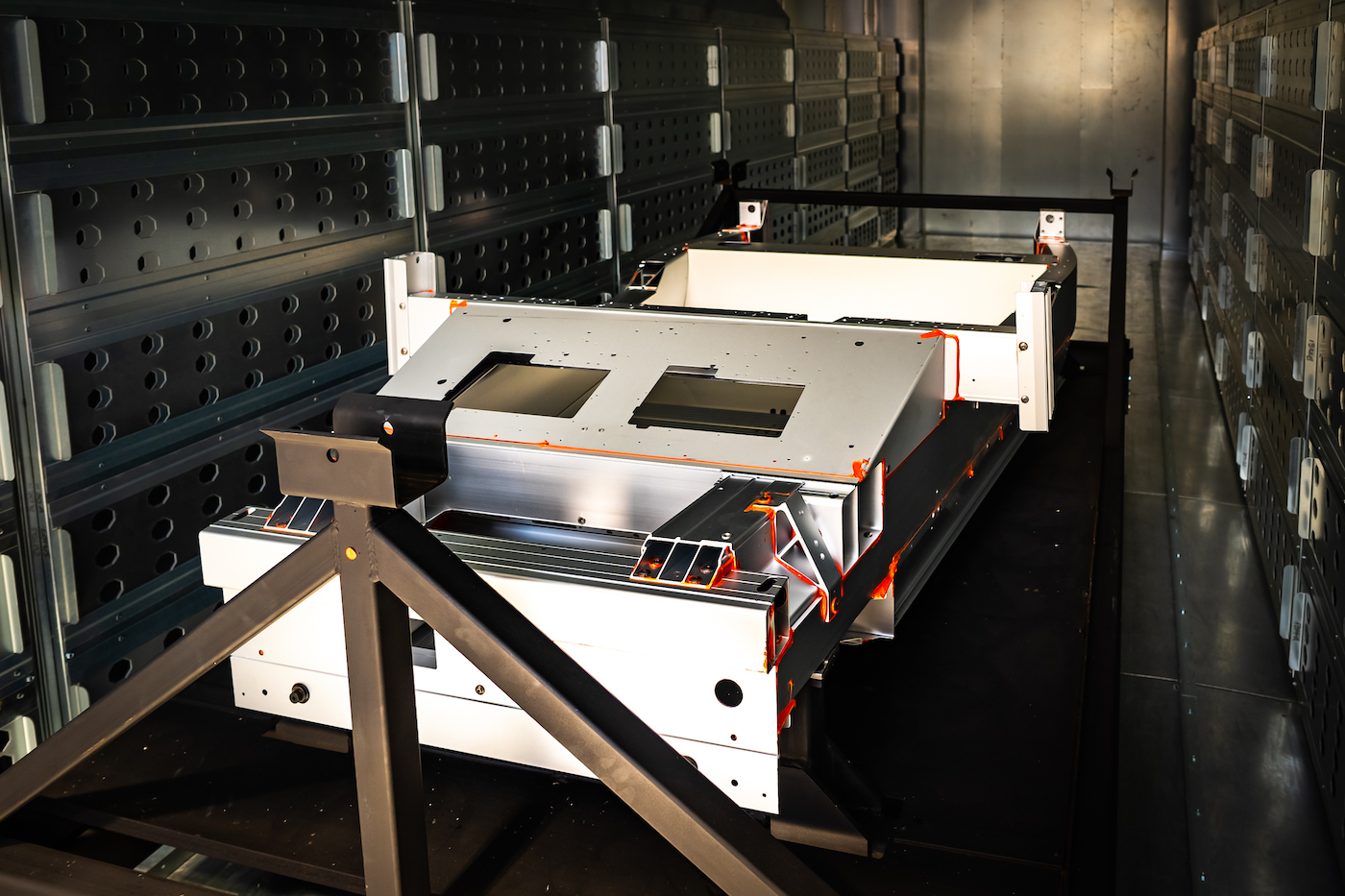