Tenneco has developed Low Emission Brake, a technology designed to help manufacturers of light and commercial vehicles, and Tier One suppliers, prepare for and meet the upcoming Euro 7 and China 7 brake emissions standards.
Tenneco says the technology meets Euro 7 and anticipated China 7 restrictions on particulate (PM10/PM2.5) emissions from vehicle brakes. The technology also enables Tenneco to utilise a variety of renewable and recycled materials and reduce C02 emissions associated with the manufacture of brake pads.
Euro 7 for light vehicles, which takes effect in 2026, is the first standard to impose limits on particulate matter emissions from vehicle brakes. The new standard restricts PM10 emissions to a maximum of 3 mg/km for PEVs, and 7 mg/km for other powertrains such as hybrids and ICE light vehicles.
The limits for heavy vans, categorised as N1 Class III, are 5 mg/km for PEVs, and 11 mg/km for other powertrains. The China 7 emissions standard, expected to be finalised by the end of 2025, will likely impose similar restrictions on brake emissions but with a focus on PM2.5.
“Preparation for Euro 7 and China 7 has required a paradigm shift in virtually every area of brake pad and disc development and manufacture, as well as significant investments in next-generation research, development and testing resources,” said Holger Schlauss, VP of global engineering at Tenneco’s OE Braking division. “Our global team has been able to leverage our unique expertise in materials science, chemical and physical analysis, and advanced analytics to meet these new requirements on behalf of vehicle OEMs and Tier One suppliers.”
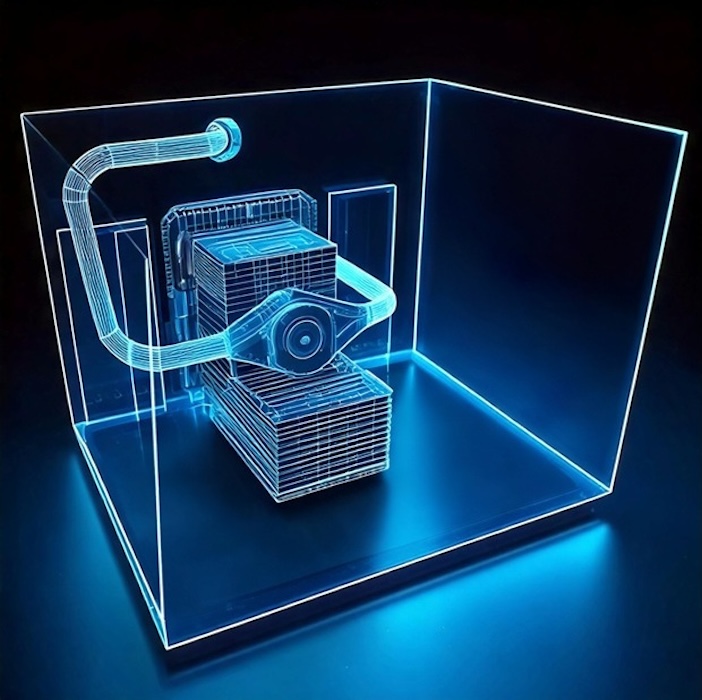
Tenneco Low Emission Brake technology has already been selected for use on a variety of upcoming passenger vehicle models from two unnamed ‘leading European automakers’. The technology uses an array of natural materials that exhibit exceptional mechanical properties, along with naturally occurring minerals and recycled raw material, to reduce particulate emissions while meeting the unique braking requirements of each vehicle model.
Tenneco engineers are also working closely with vehicle OEMs and Tier One suppliers in the development and application of highly effective and cost-efficient brake pads that further reduce PM10 emissions on coated and standard grey cast-iron brake discs.
“One of the chief benefits of these new technologies, beyond the reduction of particulate matter emissions, will be exceptional brake system performance and durability,” added Schlauss. “In fact, for some consumers the Low Emission Brake pad could last almost the life of their vehicles.”
The technology is the result of a development programme involving Tenneco’s global network of friction research laboratories, advanced testing capabilities and expert groups.
Tenneco’s global OE Braking business has focused on driving brake system innovation both through its internal resources as well as partnerships with other leading suppliers, customers, and government-sponsored working groups.
Since 2017 the company has been a member of the Particulate Measurement Program of the European Commission’s Joint Research Centre, which defines processes and standards for measuring particulate emissions, and successfully participated in the interlaboratory studies (ILS) performed by the group.
Ready for China 7
As Low Emission Brake technology is being adopted by European OEMs and Tier One suppliers, the company is also collaborating with vehicle manufacturers to prepare for implementation of the China 7 emissions standard. Tenneco says it supplies brake pads and other products to the majority of Chinese light and commercial vehicle OEMs, including Chery-Huawei, GAC Motor, Geely, FAW, Great Wall Motor, JAC-Huawei, SAIC Motor, and XPeng Motors.
“As China’s OEMs finalise plans for their 2026 and later models, we are well prepared to meet the corresponding demand for Low Emission Brake pads that are precisely matched to each model,” said Marco Frecchio, business development and supply chain senior director at Tenneco OE Braking.
In preparation for China 7, Tenneco has increased its development and testing capabilities through investments in state-of-the-art emissions dynamometers and tools covering the early-stage development process, enabling an accelerated concept validation, optimised material feasibility, and mitigated risks.
The company is also using artificial intelligence and machine learning in conjunction with virtual simulation tools to predict the influence of specific product compositions and processes in brake emissions and other critical performance measures more accurately and quickly.
Tenneco brake pad technology also increases the sustainability of pad production through the use of renewable materials and energy. As one example, the use of renewable and recycled materials and naturally occurring minerals reduces manufacturing-related greenhouse gas emissions by 15-35%. Tenneco engineers are also validating manufacturing technologies that will further cut energy consumption and CO2 emissions.