In this engineering insight piece from VDI’s late technical editor, John Miles takes a look at how Percentage Ackermann impacts chassis behaviour.
Percentage Ackermann describes the degree to which the inner and outer wheels are steering on their respective radii throughout the whole range of the steering motion. For low-speed manoeuvering, the theoretical ideal is 100%, because then each front wheel would be on its respective radius and there would be no “scrubbing” at all between the inner and outer tyres.
With zero Ackermann or parallel steer (Lotus Esprit), the inner and outer wheels are on the same lock angle at all times. As a result you will find that from mid-lock onwards there is increasing protest from the front tyres as the inner tyre is being forced to steer on the same radius as the outer one.
So more Ackermann is better for turning tight corners, but for me the intriguing part is the effect changes in percentage Ackermann can have on high-speed stability. The difference between outer and inner wheel angles at full lock with 60% Ackermann is usually about 4°, say 32° and 36°, respectively, but high-speed car control is achieved with steering wheel angles of no more than 10° or less than 1° at the wheel rim with a typical 16:1 steering ratio.
Whatever the percentage Ackermann, the difference between outer and inner wheel angles at 1° is not measurable by any means I know of, yet the effect on straight line and high-speed cornering stability of small changes in Ackermann can be substantial; the more Ackermann angle you have, the more “pointy” the car becomes at high speed.
My most recent experience of this was on a high-performance RWD car that needed faster steering response. The rack ratio couldn’t be changed, so the steering arms were altered instead, the unavoidable side effect being a reduction in percentage Ackermann from 50% to 30% at full lock, thus closer to parallel steer. With quicker steering I was concerned that there would be a reduction in stability on a car capable of nearly 322km/h (200mph). In fact the car turned out to be significantly more stable at high speeds, and, of course, it had better low-speed response as well – a true win-win modification.
How could this be, when the difference in steered angle between the inner and outer wheels at small lock angles is so infinitely small? Even the “boffins” could give no precise explanation. Some form of logic says that in the case of parallel steer the inner and outer tyres must be trying to run on the same radius, providing a degree of across-axle “scrub”, thus resistance to driver input and the car turning.
There is no such “resistance” to turning with nearer 100% Ackermann because the inner and outer tyres are tracking more or less on their respective radii. Of course none of this takes into account the effects of kinematic and compliance steer, or static toe, which may be modifying the effective dynamic Ackermann present at any given moment.
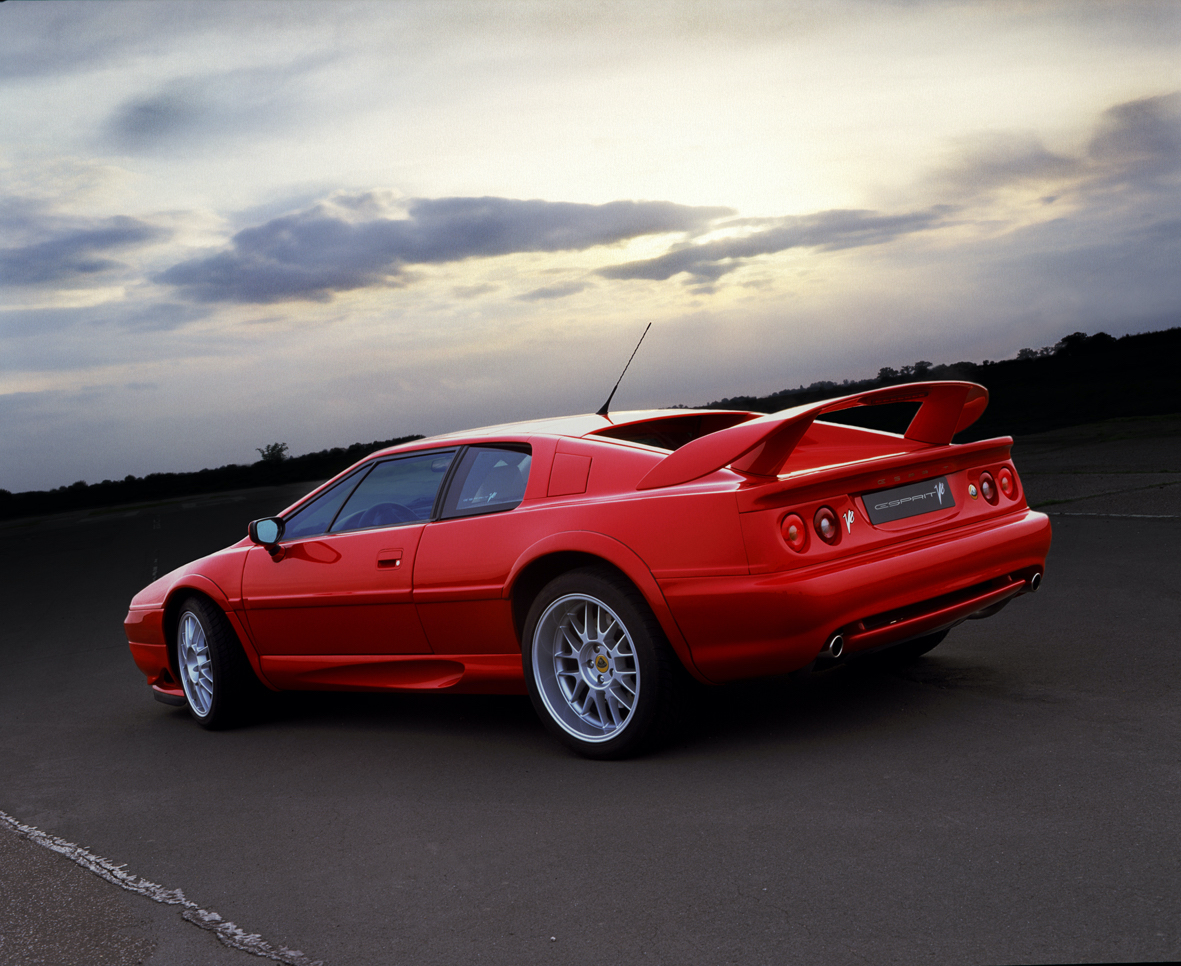
From the driving seat, the impression is that the “yaw centre” moves forward with more percentage Ackermann, and rearward with less. This can be visualised when looking at the simple top-view Ackermann drawing. Less Ackermann sees the intersection point of the steering arm pivot to steering axes moving further and further behind the rear axle centreline. It is as if the yaw centre of the car follows alterations in this intersection point to provide a longer and longer “virtual” lever arm about which the car pivots.
Years ago non-downforce race car designers favoured “parallel” steer geometries, or even anti-Ackermann, arguing that the more lightly laden inner tyre needed to run at a lower slip angle than the outer tyre to generate optimum cornering force at its lower vertical load. Of course this means the inner tyre will be trying to describe a larger radius than the outer tyre, which logic says is not conducive to the overall cornering performance. Once downforce is introduced, the inner tyre does more work and may need to run at a slip angle closer to that on the outer tyre.
Front-wheel-drive touring cars are a special case. Anecdotal evidence seems to suggest that they perform best with road-car-type Ackermann characteristics. This makes sense when you consider that the inner wheel should not be trying to drive the car forward on a larger arc than the outer wheel.
As with all chassis design, there is still a lot we don’t understand, which is why chassis development is such a challenge. Or as one renowned chassis designer said: “to be honest, choosing Ackermann angles is still guesswork”.