With an ever-evolving list of expectations by customers, how does Ford keep a model range up to date with the latest technology and safety features without compromising quality, safety and durability? Ford’s investments in driving simulations and simulators are revolutionising the way its engineers develop vehicles.
Ford aspires to leverage big data to benefit vehicle dynamics, especially in the field of simulation. Its engineers have been gathering data during various vehicle testing programmes over the years, creating a solid foundation for simulations. However, before this data can be used in simulations it must go through numerous correlation tests, which analyse the accuracy of the simulated information by comparing it with real-world data. The team can only begin building simulations when the right level of analytical capability is achieved – and only then can a simulator be built.
From the first 3D designs, to physical prototypes and finally to production, every vehicle prototype needs to pass a strict inspection process conducted by key engineers before being able to move through the vehicle development process. This process is made up of what Ford calls ‘judgement gateways’, one of which is the Final Design Judgement Gateway (FDJ), whereby lead engineers sign-off on the various improvements made to the prototype vehicles. With the addition of simulation in the product development process, the FDJ is also used for confirming the Computer Aided Engineering (CAE) modelling, ensuring that the engineers are comfortable with the results the simulation produces for various scenario tests.
For example, the vehicle dynamics team led by David Perks in Australia fully utilises simulations by using CAE as a mock-up of a real-world vehicle in order to better understand how it will behave in certain conditions. Perks’ team is confident in the simulation models, since they have been proven on numerous vehicles that have been developed out of the Ford Australia Proving Ground.
“An example of the crossover from simulation to reality is the ride of the Ford Ranger,” says Perks. “Its simulation should be able to define parts and give us the confidence that the parts will perform as they should.”
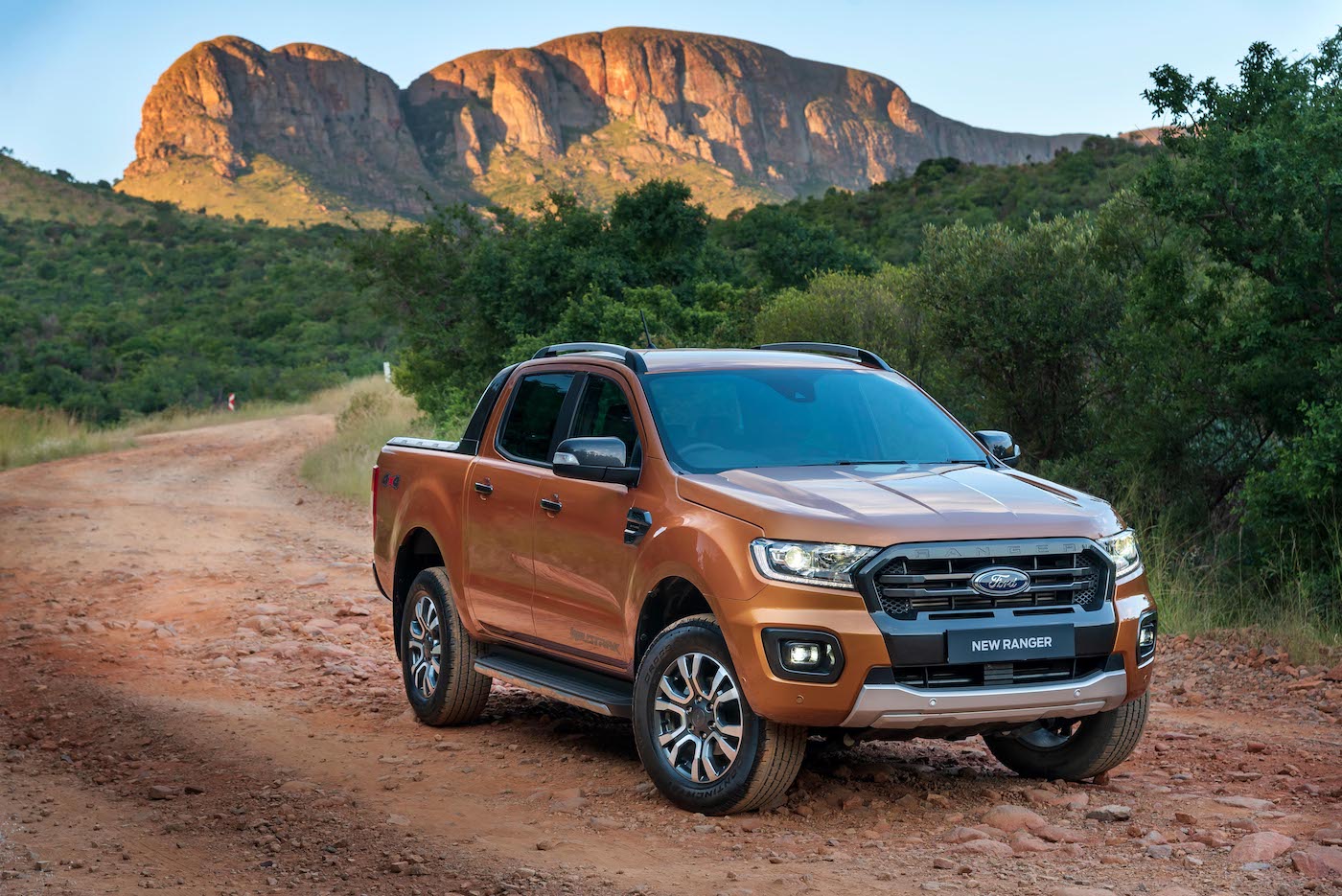
Global simulators
Simulators offer vehicle dynamics engineers the full driving experience of a vehicle, without personal safety risks, or the danger of crashing an expensive prototype. The simulators can recreate almost any driving environment, providing vehicle dynamics, sound and Advanced Driver Assist Systems (ADAS) feedback in relation to the vehicle’s behaviour.
ADAS – electronic aids which uses cameras and radar on the vehicle to assist the driver in safely operating a vehicle – are of growing importance in the automotive market. Ford’s Co-Pilot360 system offers the latest in ADAS technologies, including lane-keeping, blind spot information, automatic emergency braking (with pedestrian detection) and adaptive cruise control. These are not fully autonomous systems, but rather assistants that adapt to changing driving situations in order to enhance the vehicle’s safety systems. Being able to simulate situations where ADAS can be tuned to create a safer driving environment will benefit not just Ford drivers, but also all drivers and pedestrians nearby.
Ford has installed three simulators around the world, the newest of which is at its Australia Proving Grounds and represents the first of its kind in a Ford facility. This simulator uses a static “buck” or the vehicle’s cabin area, surrounded by large screens and projectors. When sitting in the simulator the view is similar to when you’re driving a real vehicle.
These simulators are far removed from the type you can buy in your local electronics store for playing video games on. They were specifically designed to give the highest levels of fidelity and the finest details of feedback through the steering and pedal feel. The amount of detail that needs to be processed in Ford’s simulator is immense compared to even today’s impressive racing simulation games, requiring special computers to power and analyse the simulation environment. The simulation is so detailed that NASCAR teams use the simulator at the Ford Performance Proving Grounds in the USA to help develop their race cars.
“The simulator gives us a better understanding of what the vehicle will be like when we produce a physical prototype. Since we have accurate data at the start of vehicle development, we can expect a better end-product for our customers,” says Perks.
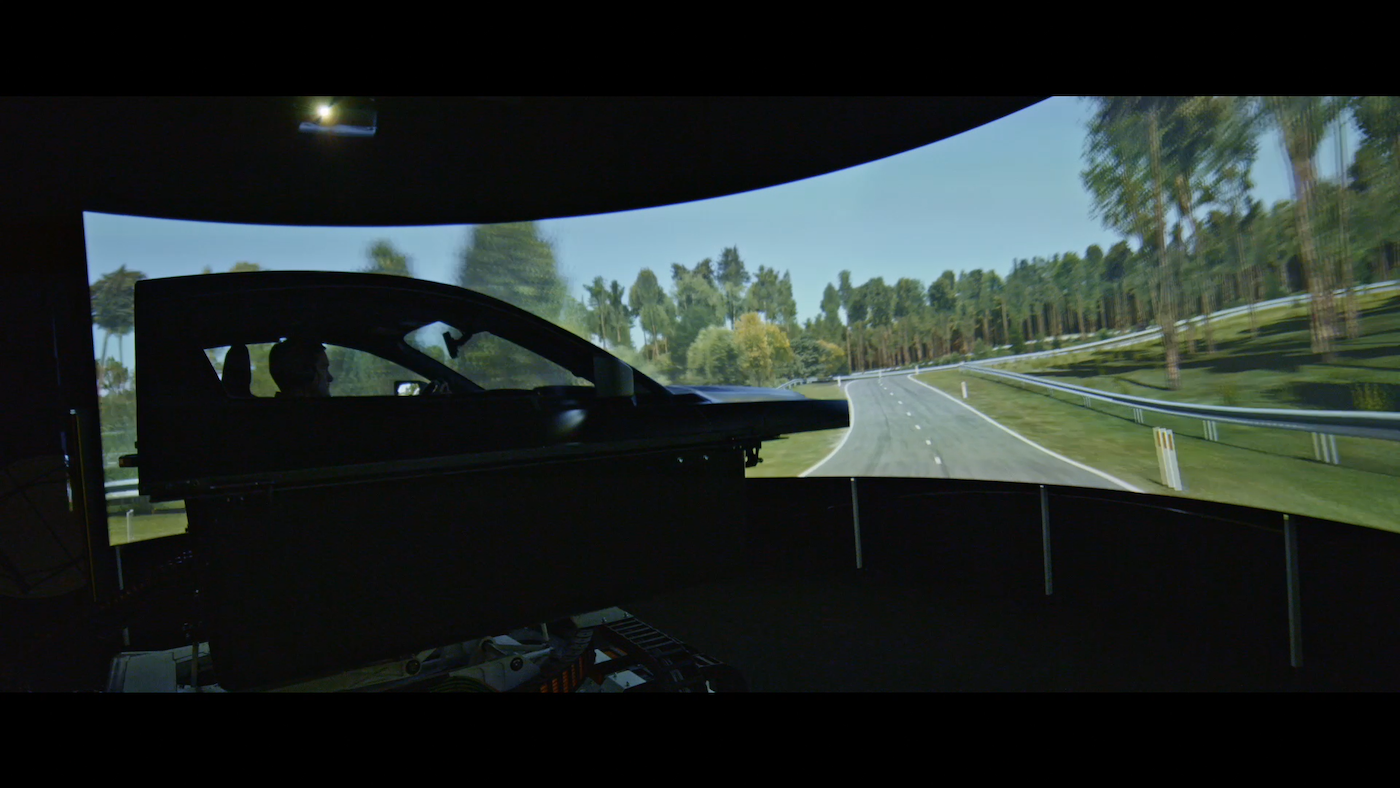
How simulations and simulators translate to passenger vehicles
Ford’s vehicle dynamics team begins work on simulator models once the wants and needs of a vehicle programme are clearly defined. Instead of going out and building a prototype, they input the data into different simulations.
“Experiencing the vehicle before it is even built will benefit us in the long run. Fewer prototypes need to be built, and in theory a more mature vehicle should be developed through the simulator, even before it is built,” explains Perks.
Simulators help slash development times and costs while also helping engineers design performance improvements for vehicles. New safety features can also be rolled out in less time; for example ADAS has been evolving quickly and the simulator gives Perks and his team the ability to tune new systems properly, so they interact naturally and best suit driver styles. It is important that ADAS gives drivers the confidence it is keeping them safe.
For overall quality, simulations give engineers the ability to see how systems interact with each other to identify problems.
“In a simulation model we can make measurements quickly and understand how components and systems interact, and identify what is causing problem,”adds Perks. “Our team used analytical simulations to introduce hydro engine mounts to decrease harsh vibrations from the engines of the Ranger and Everest in 2015. This was based off previous data analysis that we have done.”
The challenges of simulation
One great advantage of running simulations is the ability to analyse information. For example the Ranger has around 700 configurations of powertrain, driveline and cab style. It would be impractical for an engineer to be expected to sit in every configuration and drive it. However, simulation can be used to make sure that each configuration has the correct settings. These analytical tools let Ford’s engineers do the most consistent job at the highest quality, says Perks.
However, he adds that the simulator also has room for improvement. Simulations of ‘hand on’ factors like steering feel rely heavily on the perception of the driver. Physical tuning is still required to achieve the goal of the best steering feel, as it is difficult to simply put into numbers. Also, creating models of certain road surfaces that are ever-changing, such as sand, is still a challenge. Physical prototypes are still needed to ensure the accuracy of the data the simulator is producing.
The ideal vision of Ford’s vehicle dynamics team is to develop vehicles that meet all the criteria that customers would ever want, using only simulations. But they are working in a dynamic environment, with customer wants and needs constantly changing, and that’s why Ford’s products in the market are also ever-evolving.
“Ford Australia is on the forefront of the drive to be analytical and is on the forefront of vehicle dynamics,” says Perks. “I challenge our engineers to provide me with the tools and methods, so that one day we can develop a vehicle using highly accurate data for the benefit of our customers all over the world.”