While the focus of EVs was initially on their environmental benefits, their impressive levels of acceleration and torque have attracted many buyers to their performance levels. Nissan is switching the focus once more, adding optimised vehicle dynamics to its EV range. The OEM has developed e-4ORCE, an all-wheel control technology designed to assist drivers of all skill levels by providing instant torque to all four wheels and delivering balanced, predictable power.
The “e” in e-4ORCE stands for Nissan’s 100% electric motor drive system. “4ORCE” (pronounced force) refers to the vehicle’s physical power and energy, with “4” representing all-wheel control.
The system is currently in the final development stages, following private demonstrations of e-4ORCE during the 2019 Tokyo Motor Show and CES in Las Vegas using a LEAF e+ test vehicle.
The e-4ORCE system is built around dual electric motors. Until now, Nissan EVs have all used a single electric motor, typically for front-wheel drive. As Nissan moves to diversify its EV lineup, it felt that an all-wheel-drive system is a logical next step, especially with the Ariya Concept strongly hinting at a future EV crossover.
The e-powertrain control technology in the e-4ORCE test vehicle reacts to driver input with precision control claimed to be three-times faster than the blink of an eye. This swift response provides the expected instant, smooth acceleration of an EV, but also ensures that the control technology can handle a range of driving scenarios.
Nissan’s engineers transferred learnings gained from both the GT-R’s Attessa E-TS torque-split system and the Patrol’s intelligent 4×4 system to maximise power output, braking and chassis control. As Ryozo Hiraku, leader of Nissan’s powertrain and EV engineering division states, “e-4ORCE is not a successor of one, but an evolution of many.”
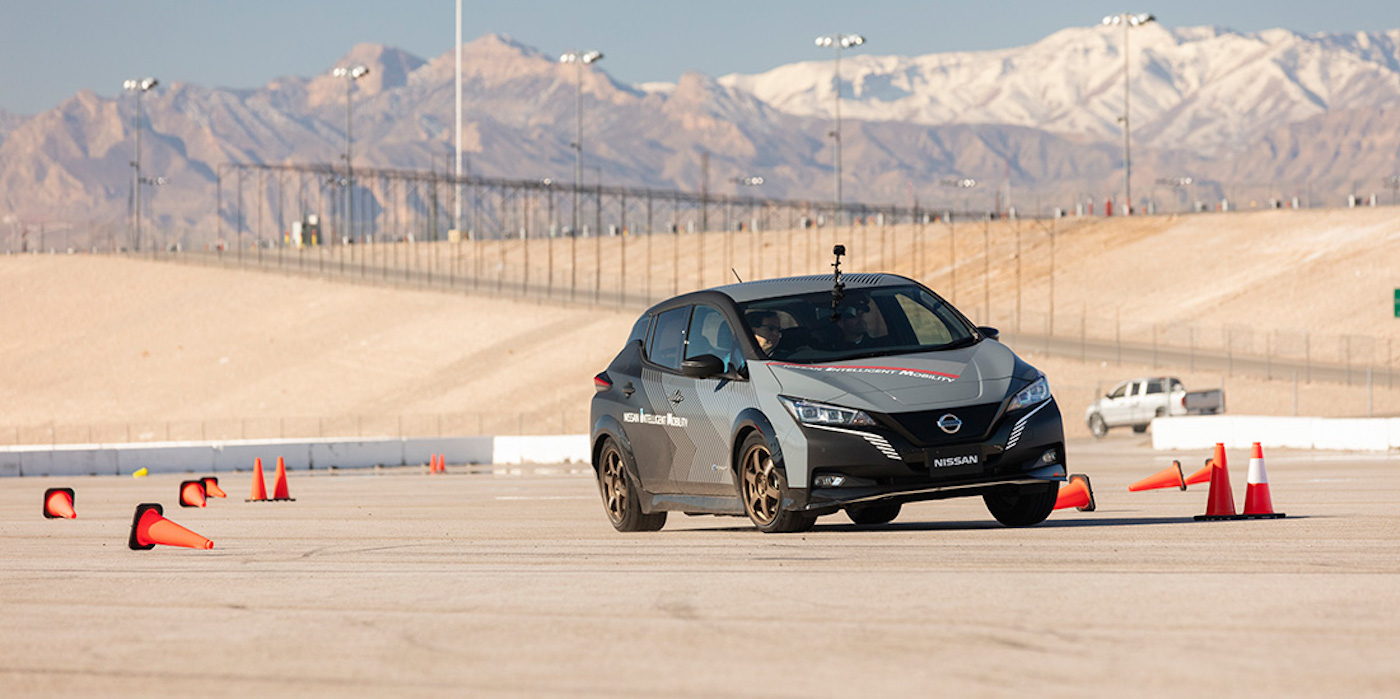
The control technology is designed to provide balanced chassis control, line tracing, and steering precision to keep vehicle behaviour predictable, even during sudden manoeuvres, enabled by constant modulation of the output of each onboard twin electric motor, as well as each wheel brake control.
As an example of how the system works, typically when turning, a vehicle tends to veer outside of the corner during acceleration, to which the driver will respond by either applying more steering input or reducing speed, which can lead to understeer. With e-4ORCE the torque is distributed to the vehicle’s front and rear wheels to maximise tyre friction (grip) according to road surface conditions and the vehicle’s situation. The all-wheel-drive balance defaults to a 50/50 distribution, but it can also transfer up to 100% of power to either the front or rear wheels, and any ratio in between, to match the road and driving conditions. Deceleration force is controlled at each wheel, though a combination of regenerative braking and hydraulic braking.
The result is a heightened level of control, especially during cornering, that provides drivers a pleasant, smooth, predictable experience with minimal steering adjustment.
Ride comfort and safety
A priority of the e-4ORCE advanced engineering team was ride comfort, with the pitch and dive created by regenerative braking being a consideration. Because the system manages braking and power to each wheel, regenerative braking is smoother, which helps keep the cabin more level.
Safety when driving on challenging surfaces, such as wet, icy or snowy roads was another issue tackled by the team, who ensured that the e-powertrain and braking system control deliver power to the wheels with the most grip while stabilising vehicle motion to maintain handling control and line traceability. If the driver applies too much power, the system will manage output to ensure control and traceability is maintained.
“We developed this technology to work in the background and not disrupt the driver,” added Hiraku. “We want even first-time drivers to feel comfortable with vehicle reactions as intended in an extremely natural way.”