Lotus has been refurbishing its assembly plant in Hethel, UK, including the final assembly building. The sports car company has worked with CPM, an Italian subsidiary of Dürr, to create an open production line that uses the ProFleet automated guided vehicle (AGV). The new assembly process will begin with the all-new Lotus Emira.
The process uses NEXT.assembly, Dürr’s modular system for final assembly, which integrates conveyors, gluing, marriage, filling and testing technology, as well as digital solutions for intelligent control of overall production.
The Hethel plant is equipped with 34 medium-sized AGVs, each with “natural navigation”, meaning that it is possible to change the AGV path, and thus also the production layout, at any time without major impacts.
The AGVs load the car bodies at the beginning of the assembly line and transport them along the entire assembly shop in stop-and-go mode: stopping at a working station for the time required to perform the necessary operations and then continuing to the next one, until the end of the line, where tests and quality checks are performed.
The latter is of most interest in terms of vehicle dynamics, as the system includes ‘x-wheel’ wheel alignment stands, which use non-contact 3D measuring technology to measure and adjust the chassis geometry to the optimum settings within angular minutes. The wheel aligners are combined with the ‘x-light’ headlamp aiming system and the ‘x-DASalign’ ADAS (Advanced Driver Assistance Systems) calibration system, which is used to calibrate the FRM (front radar module) and the FLC (forward-looking camera). The end of line is completed with the ‘x-road’ testing system, which performs final tests regarding roll mode, brake operation and ABS.
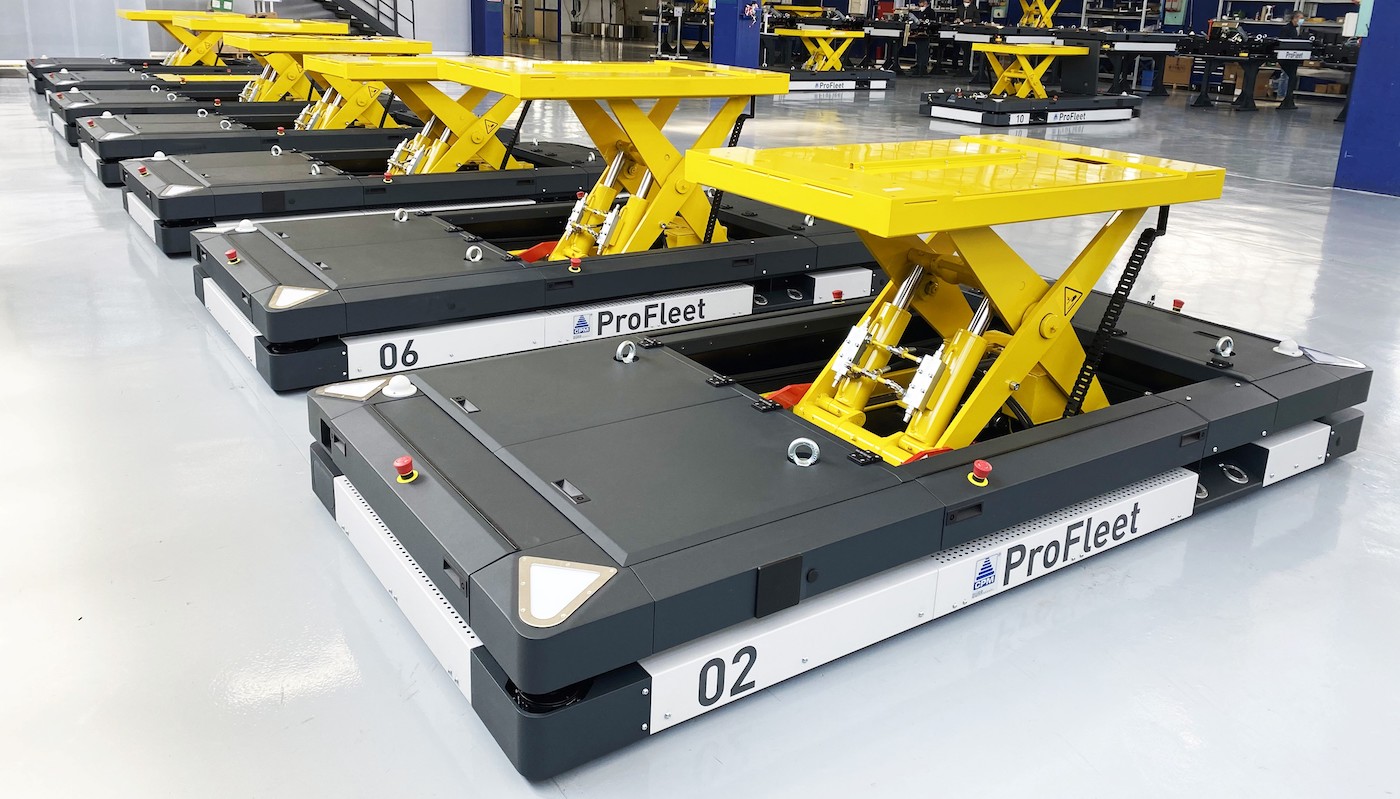
Earlier in the process, the AGVs are used for trim and final operations. The guided vehicles are provided with bi-directional kinematics and controlled by an in-house fleet management system based on an open software architecture. This setup means the plant’s operational staff can intervene directly with each AGV’s operations without having to wait for external support. The AGVs are also equipped with an electrohydraulic lifting table, which allows users to raise or lower the car body to an optimal position with high accuracy, meaning that manual operations can be carried out with safe worker ergonomics.