McLaren Automotive claims to have developed the first automotive application of a highly specialised aerospace carbon fibre manufacturing process that augments the best attributes of the material and will enhance its future models. McLaren is a company to watch in this area, as every vehicle it has ever made, from race car to road car, has been based on a carbon fibre monocoque.
The aerospace industry uses ultra-precise manufacturing methods to build highly tailored carbon fibre structures for the latest generation of commercial and military aircraft, particularly for large critical parts such as the fuselage and wings.
The methods involve the robotic depositing of composite tapes to layer structures, rather than the traditional hand layup process using pre-impregnated materials. The robotic processes make production faster, and McLaren has developed such production methods for automotive constructions and integrated them into the manufacturing capabilities at the McLaren Composites Technology Centre (MCTC) in Sheffield, UK.
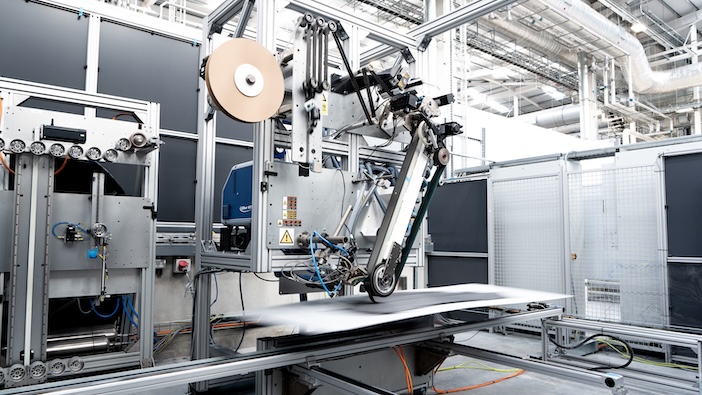
McLaren refers to the technology as Automated Rapid Tape (ART), and believes it unlocks “enormous potential” to enhance McLaren road cars with carbon fibre structures that are optimised to be lighter, stiffer and stronger, produced with even greater consistency from part to part, and produced in a manner that generates less waste material. The resulting McLaren ART carbon fibre forms are also visually distinct from conventional hand-cut pre-impregnated carbon fibre components.
The McLaren ART method is rather different to that of the aerospace industry method of using robotic arms to layer composite tapes. Instead the ART method employs a specially designed machine using a fixed deposition head and a rapidly moving bed capable of rotation, which unlocks a faster manufacturing process suitable for automotive applications and high-rate composites manufacturing.
Greater design freedom for engineers
McLaren says that ART enables tailored fibre placement, creating new possibilities relating to load bearing or stiffness requirements that are not possible using conventional methods. This tailored fibre placement opens-up innovation by freeing engineers from the constraints of a uniform material.
Specific adjustment of fibre orientation within the composite material allows for anisotropic stiffness, meaning that rigidity can be enhanced in specific directions, while flexibility can be maintained elsewhere. In short, it enables new ways to design highly loaded and complex aerodynamic components.
ART also enables improvements in strength-to-weight ratios, as the fibres can be concentrated in areas subject to high stress or load, such as joints, edges or connection points, in turn allowing for the removal of unnecessary material in low-stress regions.
Carbon fibre structures created with less waste
The measured lengths of dry composite tape are laid down when building out a part made of ART carbon fibre, significantly reducing the generation of irregular-shaped waste off-cuts that cannot be reused. McLaren says that up to 95% of the raw dry tape material used to layer a component goes into the final part.
The automated process also reduces any positioning inaccuracies and material loss caused by human error, ensuring that the final layup is within design tolerances, in turn minimising rejected parts and reducing waste. The automated element of the Automated Rapid Tape machine provides real-time monitoring and control, ensuring consistent process parameters and optimised part quality.
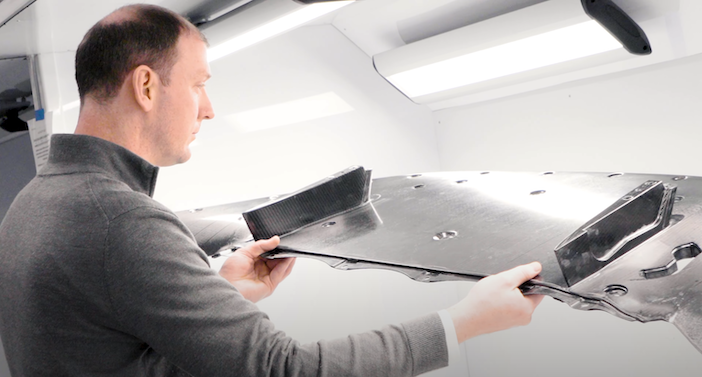
An enabler of greater use of carbon fibre
ART technology reduces manufacturing time and costs, meaning McLaren can look at using carbon fibre in more areas of a vehicle. Looking beyond the carbon tub, the wider use of ultra-lightweight body panels constructed of ART carbon fibre becomes more feasible and cost effective.
McLaren is keen to point out that this is not a future technology – ART is already integrated into its manufacturing processes. A prototype high-rate deposition machine has been installed at the McLaren Composites Technology Centre, and this first installation of ART technology will be upscaled to an industrial-specification machine later in 2025, with increased manufacturing capacity.
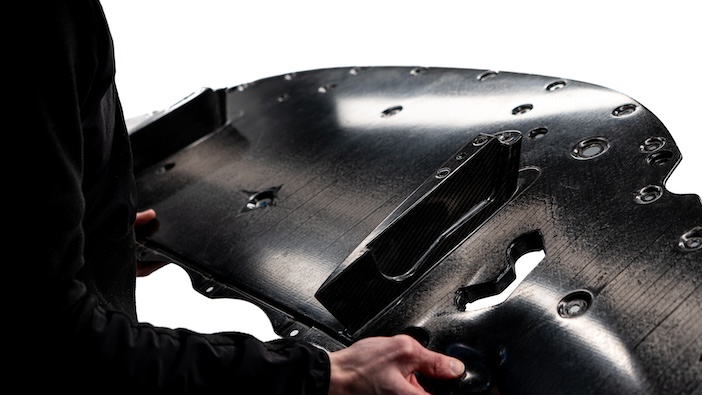
The first McLaren vehicle to feature ART carbon fibre is McLaren’s new Ultimate supercar, and the next car in the ‘1’ car linage; the McLaren W1. The fixed plane within the active front-wing assembly – an integral part of the car’s aerodynamic package that can generate up to 1,000kg of downforce – is manufactured from ART carbon, benefitting from increased stiffness.
McLaren says the ART carbon fixed-plane is up to 10% stiffer than a comparable pre-impregnated part, reflecting a significant enhancement considering its aerodynamic load-bearing function. Further components made from ART carbon fibre are under consideration for production examples of the W1.
The Automated Rapid Tape production method and ART carbon structures also unlock possibilities for the next generation of carbon fibre architectures. McLaren is currently looking at integrating the technology into the structure of an ultra-lightweight, ultra-strong carbon fibre tub that can underpin the next generation of McLaren supercars.
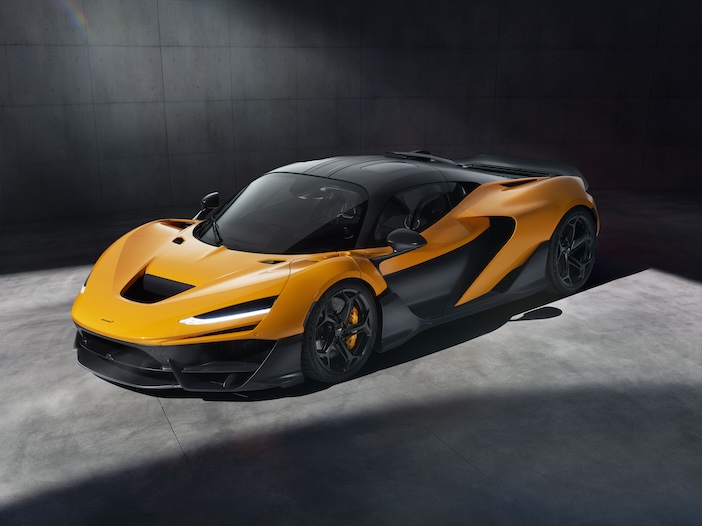