Kistler has launched the RoaDyn Racing wheel-force transducer (WFT) for motorsport testing applications. The company says this self-contained measuring wheel has an installation time of less than 60 seconds, and requires no external systems or complex setup, quickly providing users with accurate data acquisition, providing insight into wheel forces and vehicle dynamics.
Drivers of racing cars can accelerate from 0 to 100kph in 2.5 seconds, and navigate tight corners at high speeds. With such intense pressure on both vehicle and tyres in motorsport, precise data collection is crucial to prevent tyre blowouts, mechanical failures, and accidents. By monitoring tyre loads and behaviour, engineers can optimise cars to ensure the safety of drivers and spectators alike, while teams can better adapt their race strategies.
The generated data also provides insights into vehicle dynamics factors such as balance and stability. By analysing longitudinal and lateral dynamics, including sideslip and drift angles, manufacturers can fine-tune chassis and control systems such as ABS and TC, ensuring stable handling during sudden, highly dynamic driving manoeuvres.
Understanding the complex dynamics of wheel forces is essential. Advanced tools enable motorsport teams to manage the intricate balance between speed, safety, and external influences such as track temperature, weather conditions, and aerodynamics.
Kistler initially developed the new RoaDyn Racing wheel-force transducer in response to the switch from 13-inch to 18-inch wheels in Formula 1, which creates more space for sensors and electronics. The self-contained WFT device helps teams optimise tyre management, weight distribution, tyre degradation, and driving dynamics across various race series. The device is already being used in the development of the latest generation of GT3 vehicles, and a pre-series version has been tested in Formula E since 2021.
How the WFT works
The RoaDyn Racing WFT eliminates the need to connect to the vehicle’s onboard system or external transmission modules that could compromise data integrity. The WFT stores data directly within the measurement device, allowing for quick and easy downloads via USB.
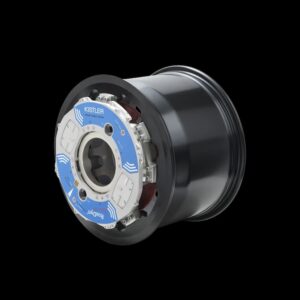
Mechanics can also use a remote control to start measurement data acquisition from all four wheels simultaneously, which simplifies and facilitates work processes. Synchronisation with the other measured values is realised by a trigger, which can be operated in both master or slave mode. The internal power is supplied by rechargeable batteries.
At the heart of this system are four highly precise, temperature-compensated strain-gauge load cells that measure forces and moments acting on the wheel of up to 20kN wheel load. These sensors provide data on tyre loads and tyre behaviour. The system calculates all force and moment components within a rotating coordinate system, then converts them into a non-rotating (fixed wheel) frame by applying the angular functions of the rotating angle.
This complex process is handled in real time directly in the wheel force transducer, ensuring instant and accurate data. If required, the system also records individual forces. Precision is further ensured through the calibration of the sensors according to ISO 17025, using the Hexapod system from Kistler.
Forged from lightweight magnesium or aluminium alloy structural components, the device is designed for durability and has undergone extensive rotational bending testing with over two million cycles at loads up to 5,000Nm. The WFT can be used at speeds of up to 360kph.
Its ring-shaped electronics provide unobstructed access to the central nut, while the independent ‘on the wheel’ electronics simplify the installation process, enabling mechanics to install the device in less than 60 seconds. The design of the WFT allows teams to handle it correctly within two hours, thanks to its simplified setup. Kistler also provides detailed instructions and offers support whenever needed.